100% Post-Consumer Bottle Flakes To Food-Grade Preforms In One Step
Written by Mr.Li. – Founder of Hop International Co., Ltd and Topwell Group.
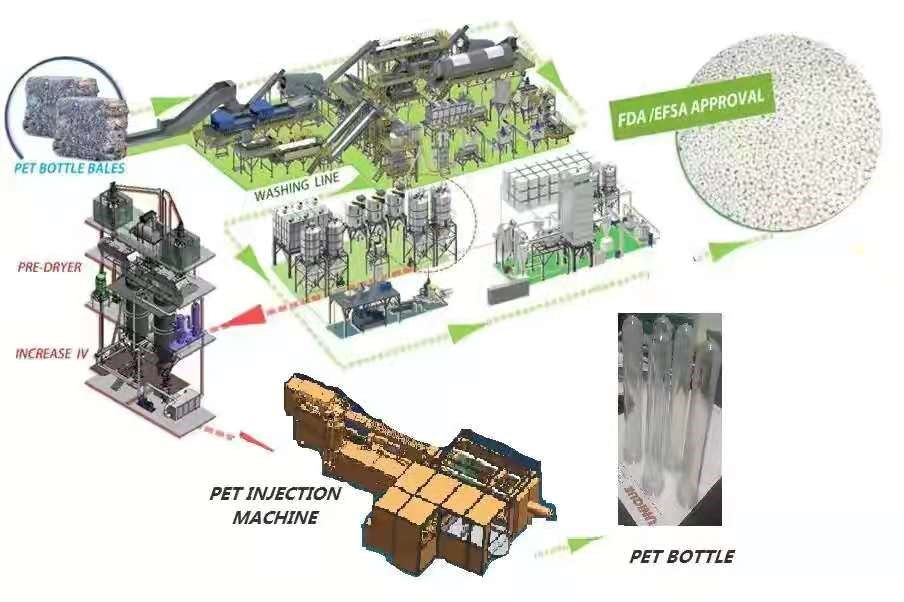
Layout of rPET flake to bottle preform line
This is a processing line which turns used PET bottle bales to rPET flake and finally to bottle preform.
The processing capacity of PET bottle bale recycling line is 3000kg/h, including: unpacking, metal removal, label removal, pre-washing of the whole bottle, automatic bottle sorting , manual sorting, crushing, floating washing, hot washing of bottle flakes, friction, rinsing, drying, dust removal, automatic flake sorting and online mixing equipment
A set of extrusion equipment can be used for online connection of preform making and bottle blowing processes. The boundary between the two sides is based on the linear viscosity detector as the dividing point (including bottle flake preheating + viscosity increasing and impurity removal + melting + online viscosity detection). Can be applied to connection: pellting line and high-viscosity food grade slicing device (including drying + online metering + melting vacuum + melt pump + backwash screen changer + underwater pelletizing + online crystallization), the design capacity is: 2300kg/ h.
Working principle and characteristics
-The PET bottle bales are sent to the belt conveyor by a crane or a clamp truck, the bottle baling wires are manually cut, and they are transported to the next bottle washing section by the belt conveyor.
-The whole bottle washing section: PET bottle bales are transported by the conveyor into the bottle washing machine. PET bottles are cleaned according to the bottle washing process requirements. During the bottle washing process, the bottle washing machine unwraps the flaky bottle bales at the same time. The bottle washing machine pre-washes and removes the sediment and impurities in the PET bottles. Can remove some PE trademarks, paper labels and some adhesive PVC labels still remaining in the PET bottle.
-More importantly, after heating and pre-washing, the physical properties of the PVC bottle changed (compared to the PET bottle, the color of the PVC bottle becomes milky white or light yellow.) It is very convenient for subsequent selection. The washing process control and the addition of the washing liquid are automatically executed by the PLC computer
– In the sorting section, the bottle passes through the manual sorting section, which can remove the heterogeneous bottles, PVC bottles, heterochromatic bottles, label scraps and garbage in the PET bottles, and ensure that the cleaner PET bottles enter the next section.
-The crusher is specially designed for PET bottle crushing. It has the characteristics of smooth feeding, stable output, low energy consumption, low vibration and noise value, strong structure, low maintenance cost, and long service life. At the same time, wet crushing eliminates the use of water. The impact force strengthens the cleaning effect of PET fragments, and reduces the friction heat due to the cooling effect of water, reduces PET fragments, and prolongs the service life of the tool
-The stages of floating washing, hot washing, friction and rinsing are the final purification of PET bottle flakes, which mainly rely on three washing forces: mechanical force, chemical force and heat, to remove the trademark, bottle cap, glue and chemical in the bottle flakes, and other impurities
Increase the viscosity of the flakes, melt and filter. After that, the food-grade melt directly enters the downstream preform forming system.
-A unique set of PET preform injection molding machine adopts unique screw plasticization and plunger metering melt filling technology to produce PET preforms. 100% recycled PET pellets can be used to produce qualified preforms. At the same time, it expands the design space of preforms, reduces weight and energy consumption, reduces AA, and reduces IV drop. It can be integrated and expanded upstream and downstream into an all-in-one machine, integrating preform injection, blowing, filling, and capping, greatly improving production efficiency and reducing operating costs.
-This system omits the production and melting process of recycled PET pellets that are necessary in the traditional process, and eliminates the risk of yellowing particles and the formation of volatile compounds. Therefore, the bottle is also significantly different from other 100% recycled PET bottles in appearance
-The online regenerated preform produced under this process can be comparable to new injection molding products. The combination of four-step process-impurity removal, IV stability, melting and injection molding-is completed in a single system, compared with traditional systems. Energy saving by 30%, while CO2 emissions are reduced by 25%, which is significantly lower than the emissions of PET bottles produced from traditional recycled PET raw materials.