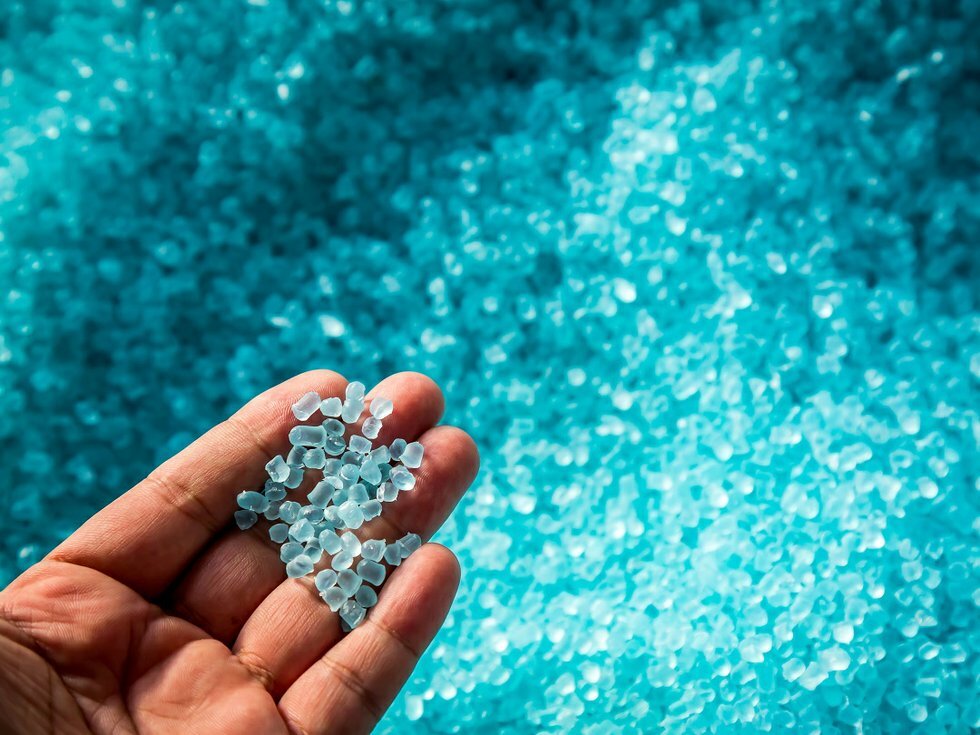
Where does plastics come from?
According to The British Plastics Federation, most of synthesis plastics used today are derived from crude oil, natural gas or coal. The process includes steps:
– Extraction of raw materials to get complex mixture which needs to be be processed;
– Refining process: converts crude oil to useful chemicals including “monomers” (a molecule that is the basic building blocks of polymers). The crude oil is heated in a furnace, then sent to the distillation unit, where heavy crude oil separates into lighter components called fractions. One of these, called naphtha, is the crucial compound to make a large amount of plastic.
– Polymerisationis: a process in the petroleum industry where light olefin gases (gasoline) such as ethylene, propylene, butylene (i.e., monomers) are converted into higher molecular weight hydrocarbons (polymers). This happens when monomers are chemically bonded into chains. There are two different mechanisms for polymerisation:
+ Addition polymerisation
The addition polymerisation reaction is when one monomer connects to the next one (dimer) and dimer to the next one (trimer) and so on. This is achieved by introducing a catalyst, typically a peroxide. This process is known as chain growth polymers – as it adds one monomer unit at a time. Common examples of addition polymers are polyethylene, polystyrene and polyvinyl chloride.
+ Condensation polymerisation
Condensation polymerisation includes joining two or more different monomers, by the removal of small molecules such as water. It also requires a catalyst for the reaction to occur between adjacent monomers. This is known as step growth, because you may for example add an existing chain to another chain. Common examples of condensation polymers are polyester and nylon.
– Compounding/Processing
+ In compounding, various blends of materials are melt blended (mixed by melting) to make formulations for plastics.
+ Generally, an extruder is used for this purpose which is followed by pelletising the mixture. Extrusion or moulding process then transforms these pellets into a finished or semi-finished product.
+ Compounding often occurs on a twin-screw extruder where the pellets are then processed into plastic objects of unique design, various size, shape, colour with accurate properties according to the predetermined conditions set in the processing machine.
There are many different types of plastics, and they can be grouped into two main polymer families:
- Thermoplastics (which soften on heating and then harden again on cooling).
- Thermosets (which never soften once they have been moulded).
Thermoplastics | Thermosets |
Acrylonitrile butadiene styrene (ABS) | Epoxide (EP) |
Polycarbonate (PC) | Phenol-formaldehyde (PF) |
Polyethylene (PE) | Polyurethane (PUR) Unsaturated polyester resins (UP) |
Polyethylene terephthalate (PET) | |
Polytetrafluoroethylene (PTFE) | |
Polyvinyl chloride (PVC) | |
Polymethyl methacrylate (PMMA) | |
Polypropylene (PP) | |
Polystyrene (PS) | |
Expanded Polystyrene (EPS) |
Read more about different types of plastics and their recycling possibilities.